The electronics industry’s quest for higher performance and greater speed continues to intensify, driving growing complexity in front end semiconductor chip architecture. Demand for denser connections, in turn, creates new and evolving requirements for its connecting substrates.
“Through KLA’s comprehensive portfolio of direct imaging, automated optical inspection, automated optical shaping, metrology, UV laser drilling, inkjet and additive printing, chemistry process control, and software solutions, IC substrate manufacturers can maximize yield and reliability throughout the fabrication process.”
Arik Gordon, vice president, Strategy and Growth, EPC Group, KLA
What are IC Substrates, and Why Now?
Integrated circuit (IC) substrates deliver powerful connections between the nano world of semiconductor chips and the micro world of printed circuit boards (PCBs). Essentially, the IC substrate (ICS) is a base for the overall chip package — playing a role in protecting and supporting the chips inside the package as well as providing connectivity between the packaged chips and the PCB below. They are composed of several laminate layers and, usually, a supporting core in their middle. ICS contain denser drill holes and conductor paths than PCBs, which are the final boards on which all modules and packages are mounted.
The front end roadmap for transistor density continues to follow Moore’s law, but faces challenges to keep pace with meeting all the diversified demands. In recent years, there has been an acceleration of technical innovations in IC packaging and IC substrates to complement front end wafer fabrication technologies to meet performance, power and cost requirements. With the scaling of interconnect geometry throughout the semiconductor ecosystem, there is significant opportunity to bridge methodologies for both process and process control across the three worlds of front end, packaging and substrates. These once completely separated domains are becoming integrated just like the packages and systems they create.
ICS offers an aggressive technology roadmap to meet new performance requirements, and investments in this area will lead to significant growth. The total value of the advanced ICS market is expected to grow at a rate of 12% CAGR from $12.6 billion in 2021 to $24.3 billion in 2027, according to Yole Intelligence in 2022.
Key Drivers of ICS Demand
ICS players are continuously advancing their packaging technologies to meet evolving stringent requirements for smaller footprints, higher performance and lower power consumption. Trends driving ICS demand include:
- Demand for consumer electronics and mobile communication devices, requiring electronics manufacturers to deliver more compact and portable products with improved functionality. Innovative advanced packaging technology is required to fit high-performing chips into smaller spaces due to the uptrend of miniaturization in mobile device applications.
- The advent of 5G, which influenced the demand for chip packages that rely on ICS technology like flip-chip ball grid array (FCBGA) over the past few years, is expected to continue as 5G base stations continue to increase in countries adopting advanced communication technology.
- A growing demand for high-performance computing (HPC), driven by advanced AI applications, among others. It is important to note that miniaturizing is not a goal for data center servers; the focus is on maximizing performance. In fact, HPC ICS units are becoming larger.
What are Advanced IC Substrates?
The most common advanced type of ICS is a rigid substrate made of polymer laminate-type materials, such as bismaleimide-triazine (BT), resin reinforced with fiberglass (often called a prepreg), Ajinomoto Build-Up Film (ABF) or molded interconnect substrate (MIS). Advanced ICSs are used in a wide variety of packaging schemes, including many that combine multiple chip types into one advanced package.
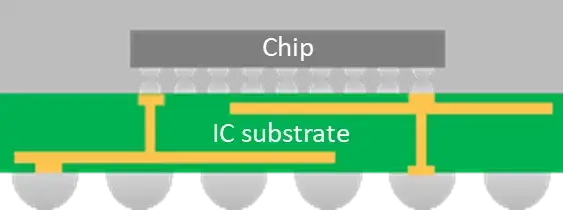
The FCBGA package is a commonly used type based on an ICS, and is implemented in a wide variety of applications such as 5G, data centers and automotive electronics. The ABF substrate represents around 83% of the total IC substrate revenue in 2022, according to Yole Intelligence, and more than 95% of FCBGA packages use ABF substrate.
What Is the Difference Between Core and Coreless IC Substrates?
Core IC substrates, also known as “build-up” substrates, are constructed with a core layer made of a rigid material, such as epoxy resin or fiberglass-reinforced laminate. The core layer provides mechanical strength and stability to the substrate. Typically, multiple layers of insulating materials and conductive traces are built on top of the core layer using a sequential build-up process.
Coreless IC substrates, as the name suggests, do not have a central core layer. Instead, they are constructed using only layers of insulating materials and conductive traces, which are built up sequentially. Coreless substrates are generally thinner and more flexible compared to core substrates. Due to their flexible nature, coreless substrates are suitable for applications where space is limited or when there is a need for flexibility, such as in wearable devices or compact electronics.
Why Are ICS Product Yield and Reliability So Important?
As the complexity of front end chip architecture continues to evolve, IC substrates are also expected to offer more connections to support improved performance, using advanced technology with finer patterning of lines and spaces as well as smaller holes called vias to meet evolving requirements. ICS manufacturers must balance ramping new integration schemes containing smaller feature sizes with high-quality requirements. IC substrates are used in high-value multi-die packages where one bad chip or a faulty substrate can kill the entire device.
In ICS manufacturing, product yield and reliability have become crucial for economic viability, market competitiveness, customer satisfaction and long-term success, not only for the ICS manufacturers themselves but also for the manufacturers that will integrate the substrates in the chip packages downstream. Here are some of the reasons:
- Cost-effectiveness: ICS production yield directly impacts the cost of manufacturing. Higher yields mean more functional substrates can be obtained from the panels, reducing overall production costs. This is particularly significant considering the complex and expensive fabrication processes involved in manufacturing.
- Profitability: Yield directly affects the profitability of ICS manufacturers. Higher yields result in more sellable substrates, increasing revenue and profit margins; low yields can lead to financial losses, especially when dealing with expensive semiconductor technologies.
- Time-to-market: Ramping a new technology quickly to a high product yield delivers faster time-to-market, which is essential in competitive industries. Manufacturers can meet customer demand promptly, launch products on schedule and stay ahead of competitors. A delay caused by low yield can result in missed market opportunities.
- Product reliability: Dependability is critical for the performance and reputation of IC products. Customers expect their devices to function properly over an extended period. High product reliability reduces the occurrence of failures, malfunctions and returns, improving customer satisfaction and brand reputation.
- Longevity and sustainability: Many applications, such as aerospace, defense and industrial systems, rely on ICs that operate reliably for several years or even decades. Reliable ICS contribute to the longevity of these systems, reducing maintenance costs and minimizing the environmental impact of premature replacements.
- Quality control: High product yield and reliability are indicative of effective quality control processes. By monitoring and improving yield and reliability, manufacturers can identify and rectify issues in the manufacturing process to drive consistent quality standards and reduce waste.
To learn more about KLA’s solution for IC substrate production, click here.
Part II of our IC Substrates 101 series covers yield-critical challenges ICS manufacturers should tackle to enhance their competitiveness, drive higher yield rates and position themselves as leaders in the industry.
Follow Us