Imagine if manufacturers could reduce design-for-manufacturability (DFM) analysis time by 96% and, ultimately, the time to market for complex PCBs.
Computational power is one of the biggest challenges in speeding up these processes because PCB manufacturers typically run DFM analyses on premises today. But what if the DFM process was moved to the cloud, where compute power is almost infinite? And, what if high-density PCBs for 5G, miniLED, advanced packaging or automotive electronics could hit the market faster as a result?
“Imagine if manufacturers could reduce design-for-manufacturability (DFM) analysis time by more than 90% and accelerate the time to market for complex PCBs. You can bet these are top-of-mind issues for most PCB manufacturers, especially those doing mass production.”
Eran Lazar, general manager, Frontline division, and vice president, KLA
Moving to the Cloud with Frontline Services
KLA develops CAM, engineering and industry 4.0 software that makes production processes faster and smarter to seamlessly handle the high volumes of data generated. Although operators can act and make changes more quickly with this software, bottlenecks are still created during DFM analysis due to complex algorithms.
When we dig into the DFM analysis process, it becomes clear that bottlenecks result from a lack of computational and processing power. Add to that server and operator downtime, and now there are even bigger bottlenecks.
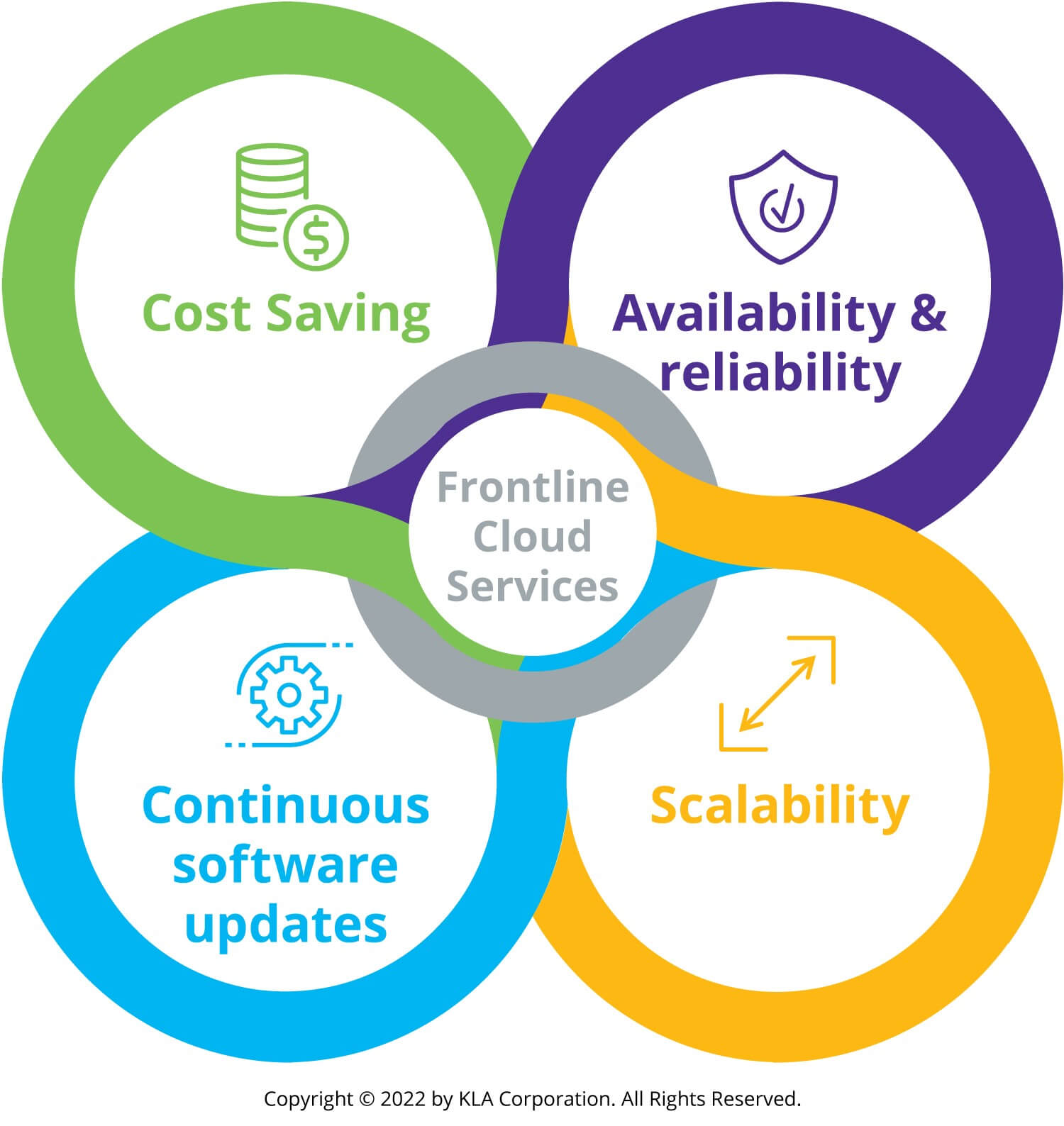
How does Frontline Cloud Services improve the process? The cloud delivers almost infinite computational power on demand, helping companies analyze more DFM checklists both serially and in parallel.
In the cloud, the DFM analysis software can also process data faster and more accurately, and it frees up manufacturers’ servers. With that shift, CAM operators can do other tasks instead of sitting idle while DFM analyses run. Now, operators can review DFM analysis results right away while other analyses run in the cloud. Ultimately, moving to the cloud unlocks two typical DFM analysis bottlenecks, benefitting PCB manufacturers and their end-customers.
First, some PCB manufacturers may be concerned with security in a cloud environment because many mass-production manufacturers work with highly confidential data from some of the world’s top PCB makers. Frontline Cloud Services resolves this concern by securing access to the cloud and using a public cloud service that validates security at the highest level.
Second, cloud computing reduces IT costs, maintenance and capital investments in hardware. Servers and software for each operator are expensive to maintain and the hardware is often five to 10 years old. Shifting DFM analysis software to Frontline’s SaaS (software-as-a-service) model with computation in the cloud virtually eliminates these issues.
What Customers are Saying
According to a customer that tested Frontline Cloud Services, running the DFM analysis for a miniLED device PCB takes up to nine hours on premises. When the customer moved the DFM analysis to the cloud using Frontline Cloud Services, processing time for the highly complex PCB was cut to 20 minutes, which is 96% faster.
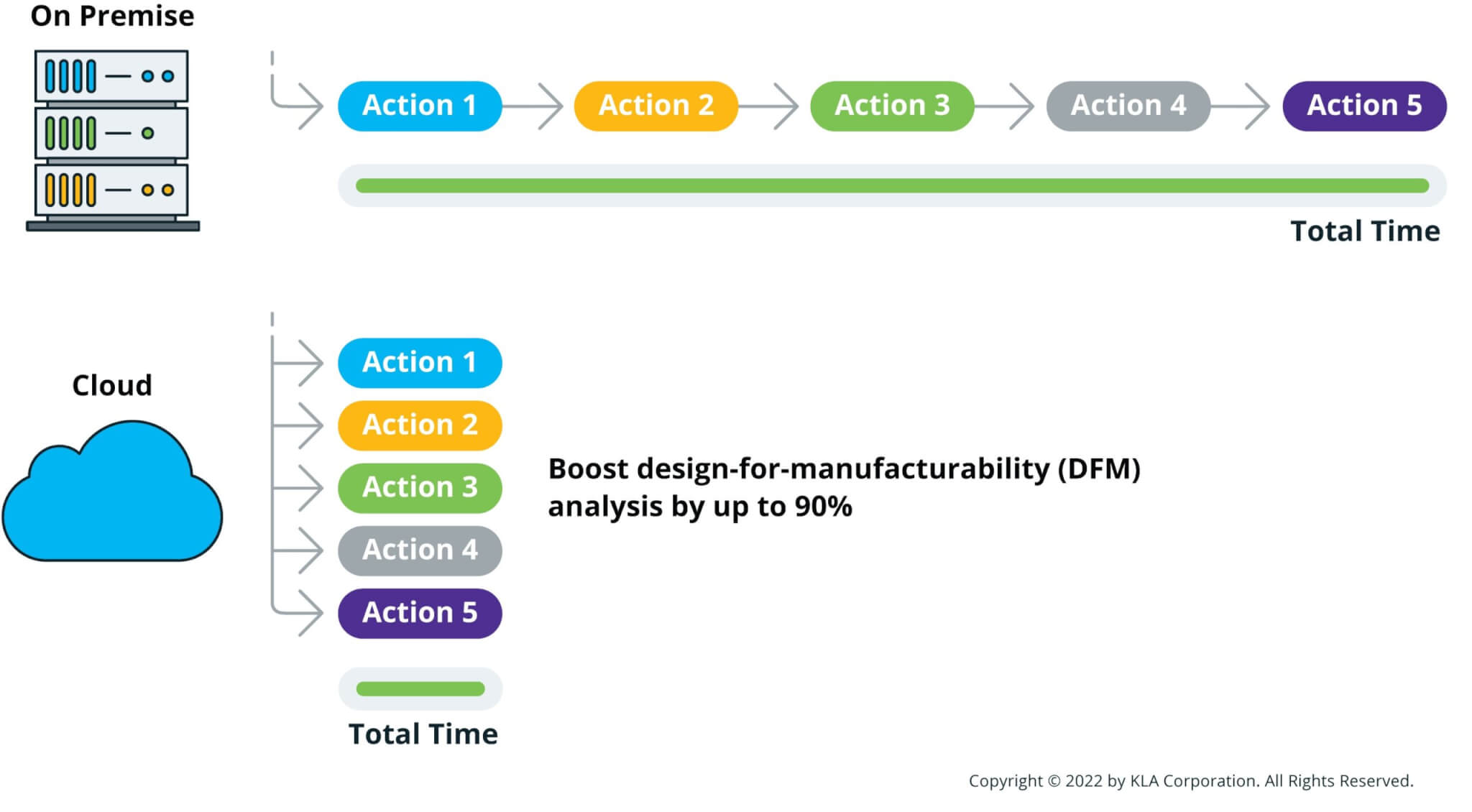
In another example, a customer manufacturing high-density interconnect (HDI) PCBs shortened design analysis time from 75 hours to only 30 minutes – 90% faster! Both examples are huge improvements, speeding up design verification, saving operators time and reducing time to market.
Fabricators continually seek ways to increase volume for each end-customer and, as a result, improving yield and boosting time to market become increasingly important.
With Frontline’s new cloud capabilities, manufacturers can run more DFM analyses in parallel, reduce downtime for operators and increase output. This benefits everyone in the electronics supply chain – fabricators and their customers as well as electronics device makers – by delivering faster time to market and higher quality electronics at lower costs.
We continually explore new ways to use the computational power of the cloud, such as adding artificial intelligence (AI) to DFM analysis, which could boost the DFM analysis process even more.
To view a press release on KLA’s Frontline Cloud Services, click here.
Follow Us